Reference cases:
Where Genano VOC abatement is needed
Here are some examples of industries where Genano has helped companies reach new levels of energy efficiency while fulfilling the emission limits.
Solvent abatement in flexoprinting with low operation costs
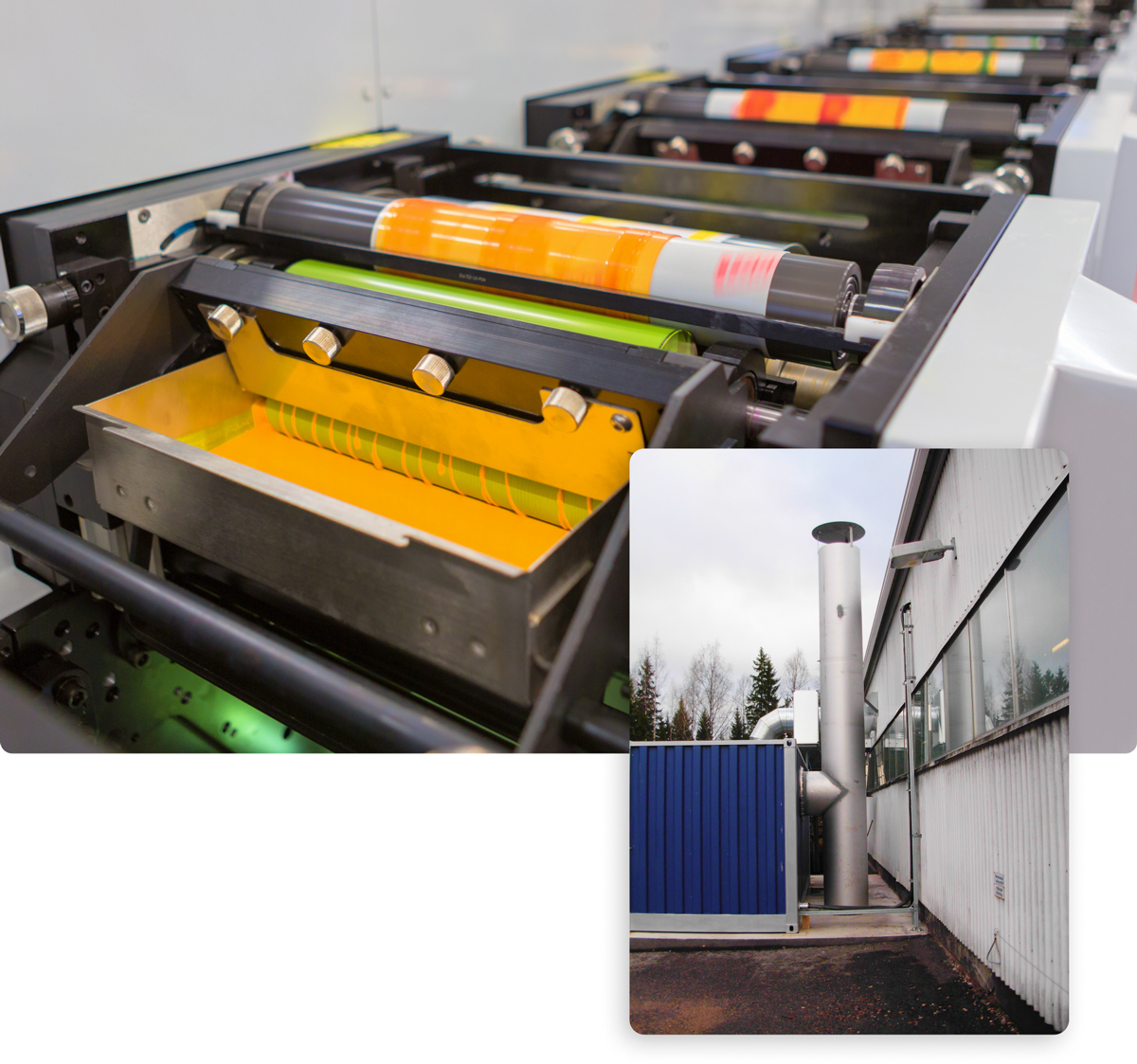
Starting point:
Customer didn’t have any abatement system for VOC emissions. Without abatement system they didn’t meet the emission limits. They chose catalytic oxidizer due to it’s lower operation cost.
Solution:
Regenerative catalytic oxidizer from Genano was installed in 2007.
Air flow 15 000 Nm3/h and the unit was installed into a 20’ container. Duration of the installation was 3 days.
Auto thermal operation >0,75 g/Nm3 (no extra heating energy).
Results:
When the printing process is on, RCO is working auto thermally. Emission limit 100mg/Nm3 has been reached and original catalyst beds are still working.
Process data:
Air flow: Max 15000 Nm3/h |
VOCs: Ethyl Acetate, Ethanol, Acetone and others |
Concentration: 1 - 4 g/Nm3 |
Emission limit: 100 mgC/Nm3 |
Solving carbon monoxide problem in pipe manufacturing
Starting point:
A supplier of different types of pipes for the energy industry had a problem with Carbon Monoxide emissions from their production.
Solution:
Genano's regenerative catalytic oxidizer with an air flow of 6000 Nm3/h was installed into a 20’ container. Duration of installation was 5 days.
Results:
Outlet emission: <80 mgC/Nm3
RCO is working auto thermally which means no extra heating is needed. Original catalyst are still in use.
Process data:
Air flow: max 6000 Nm3/h
VOC: Carbon Monoxide
Concentration: 1 – 2 g/Nm3
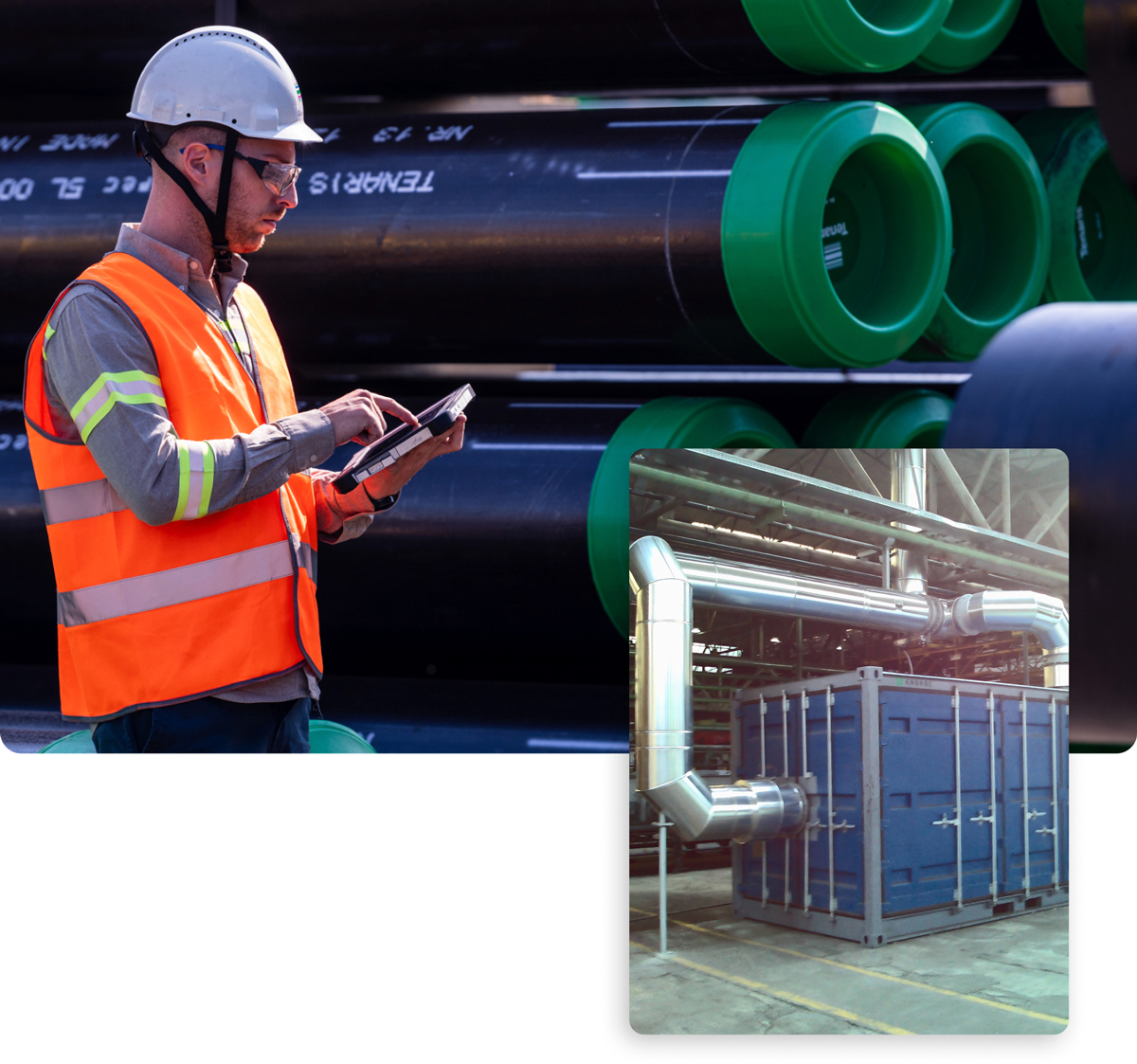
Reduced heptane levels in automotive industry
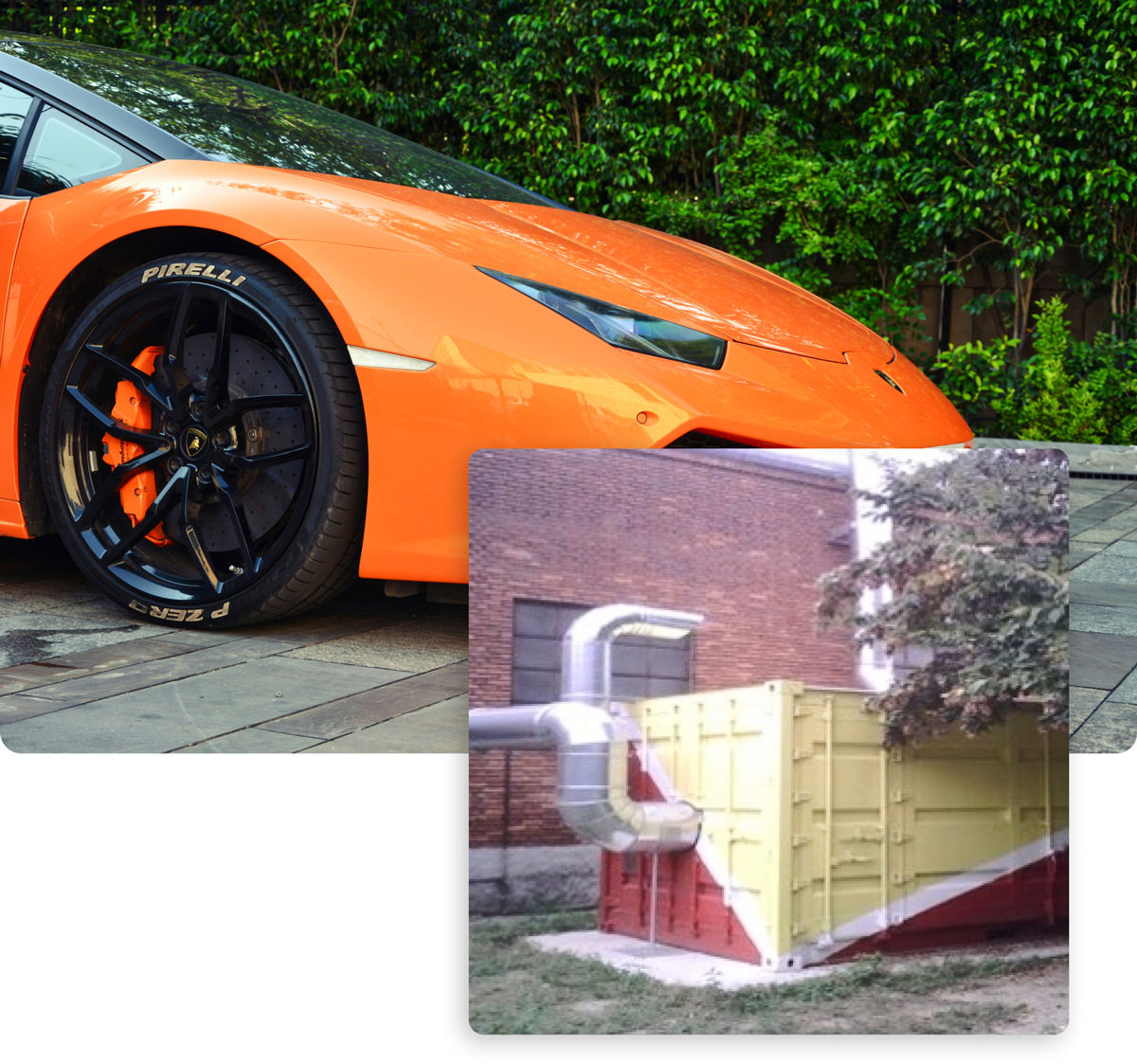
Starting point:
A tyre manufacturer had a problem with VOC emissions, especially heptane and odors. Their VOC concentration varies from 0,5 g/Nm3 up to 2 g/Nm3 and air flow is 8000 Nm3/h.
Solution:
A 8000 Nm3/h regenerative catalytic oxidizer was installed into a 20’ container. Duration of installation at customer's site was 5 days.
Results:
Outlet emission reduced <20 mgC/Nm3 and odor levels decreased significantly. Auto thermal point is 0,8 g/Nm3 and when the concentration exceeds that, no extra heating energy is needed. Original catalysts are still in operation.
Process data:
Air flow: 8000 Nm3/h |
VOCs: Heptane and odors |
Concentration: 0,5 - 2 g/Nm3 |
Chemical Industry benefits from regenerative catalytic oxidizer
Starting point:
Chemical company had a problem with their VOC emissions (AN, MMA, EB and SM). Air flow is 3100 Nm3/h. VOC concentration varies from 0,3 g/Nm3 up to 3 g/Nm3
Solution:
Regenerative catalytic oxidizer with hot by-pass. Air flow 4000 Nm3/h. The RCO was installed into a 20’ container. The installation took 5 days.
Results:
Purification efficiency has varied 95% - 99% and the energy consumption has been low.
Process data:
Air flow: 4000 Nm3/h |
VOCs: AN, MMA, EB and SM |
Concentration: 0,3 - 3 g/Nm3 |
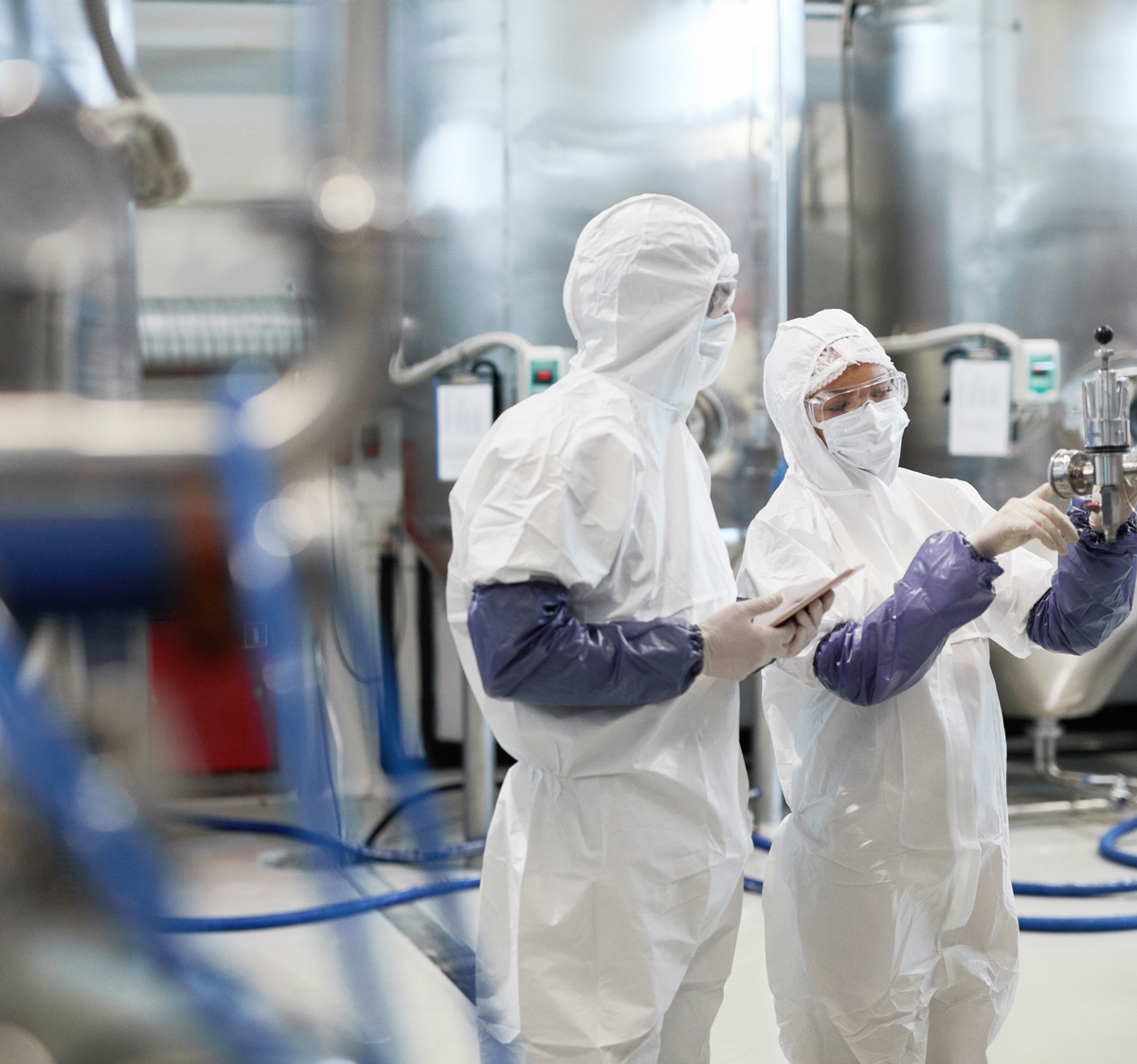
Lowered emissions with RCO in Special Paper Printing
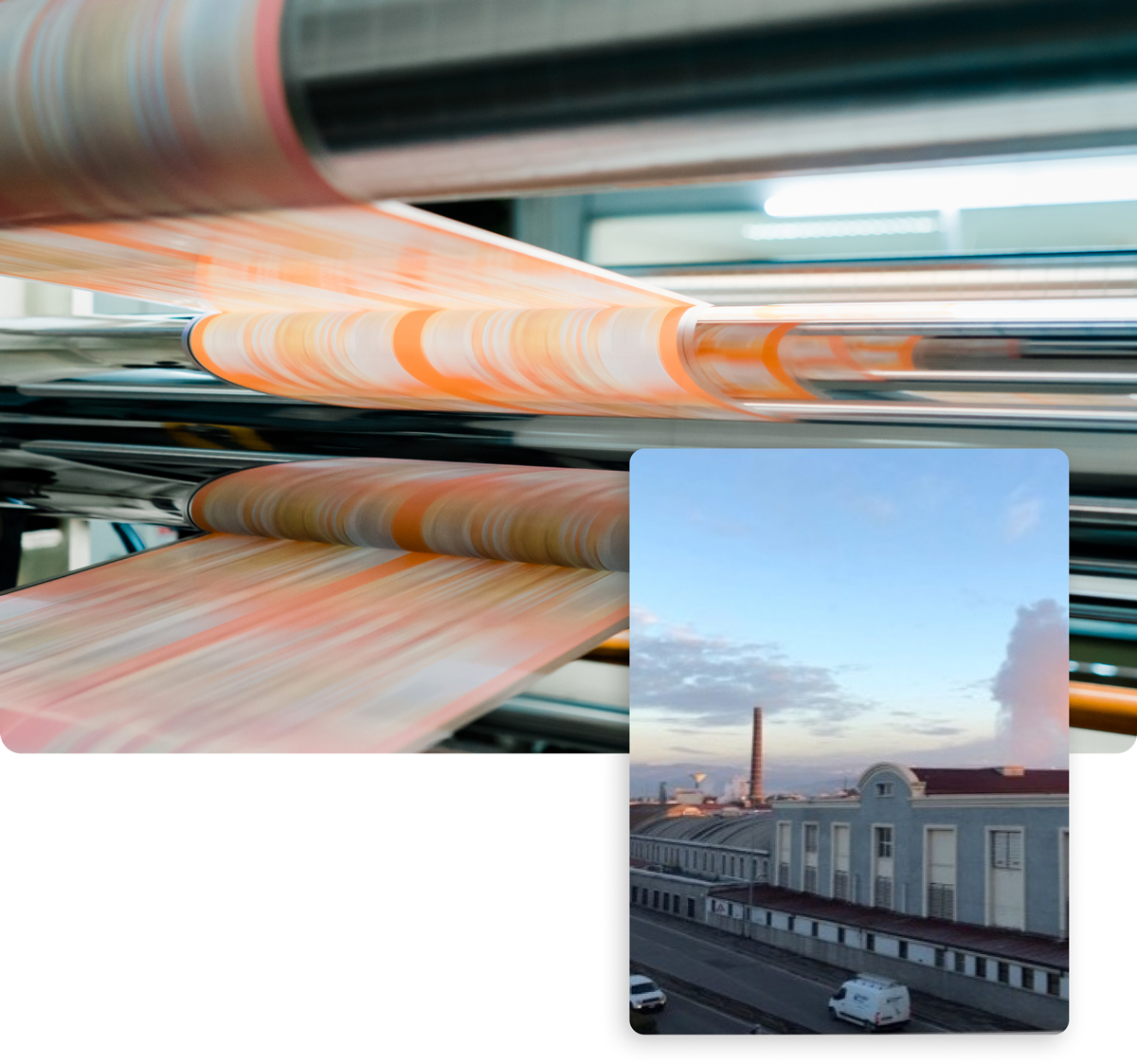
Starting point:
Special paper printing was faced with higher production and emissions requirements.
Solution:
3 chamber RCO
Result:
Emissions < 50 mgC
Process data:
Volume: 25.000 Nm3/h |
VOCs: Ethyl Acetate, Isopropanol , Etanol |
Concentration: 1800-4200 mg/Nm3 |
Energy: Autothermal point |
Solvent emission abatement in painting line for turbines
Starting point:
The turbine painting line must adopt a VOC abatement system due to solvent emissions during the painting of parts and metal sheets, essential for meeting emissions requirements.
Solution:
2 chamber Genano regenerative catalytic oxidizer (RCO) was installed.
Result:
Emissions < 50 mgC
Process data:
Volume: 4.500 Nm3/h |
VOCs: Toluene, Xilene, Nafta, Acetone |
Concentration: 1000-2000 mg/Nm3 |
Energy: Autothermal point |
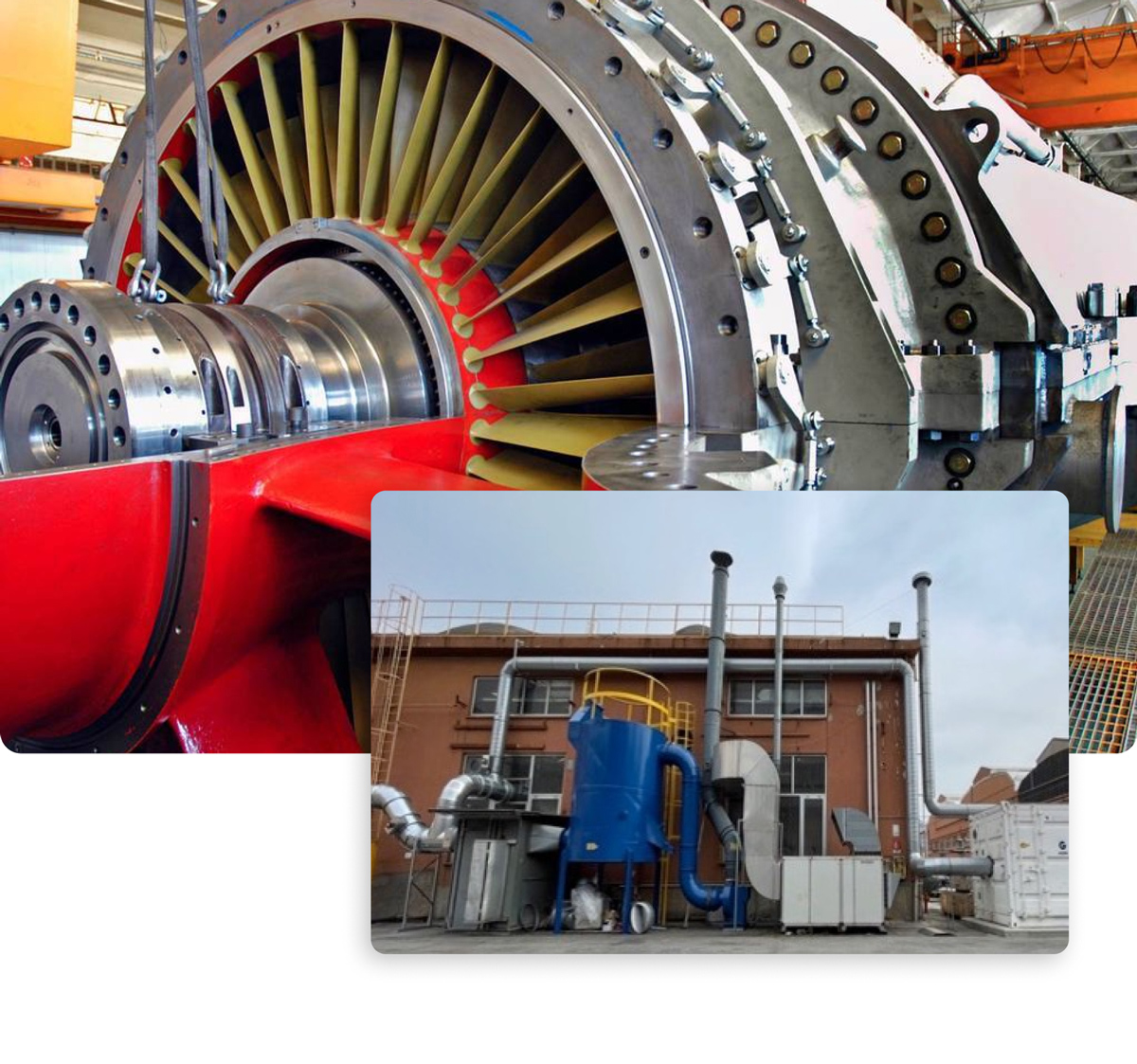
Genano RCO cuts tire production emissions
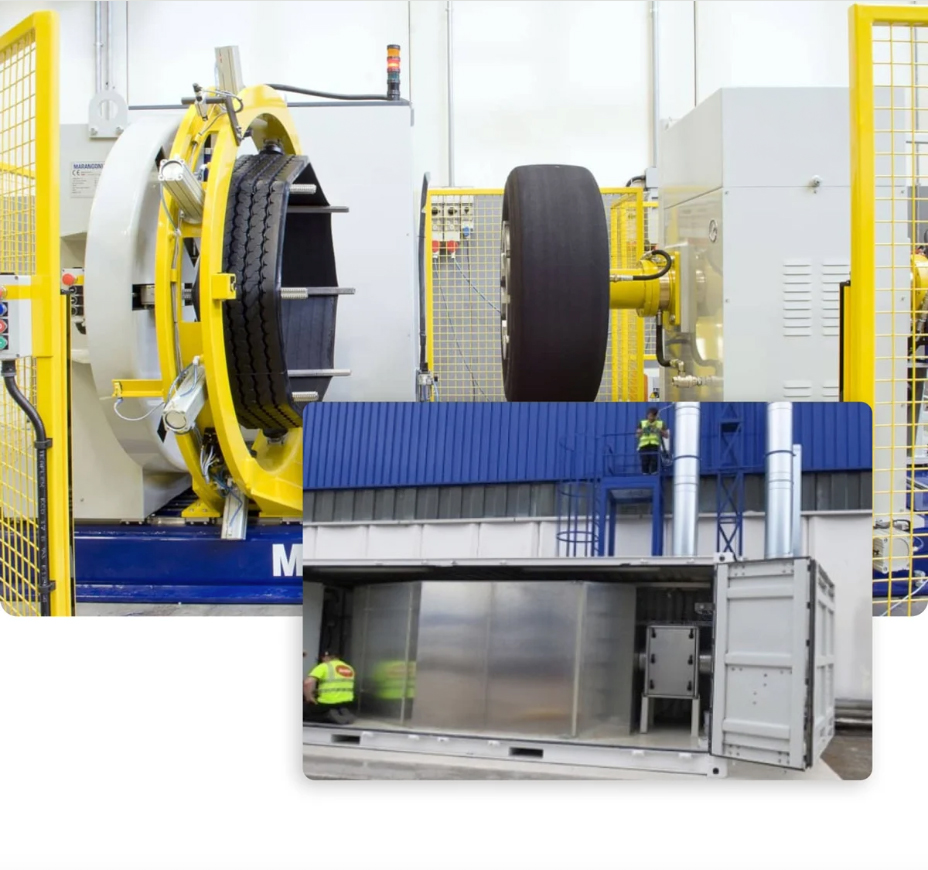
Starting point:
In tire manufacturing the use of tire adhesives causes emissions and odors that were necessary to remove with advanced VOC abatement technology, ensuring a more environmentally friendly production process.
Solution:
Genano installed a 2 chamber Genano regenerative catalytic oxidizer (RCO) to reduce emissions and odors.
Result:
Emissions < 100 mgC
Process data:
Volume: 5.000 Nm3/h |
VOCs: N-Heptane |
Concentration: 2000 mg/Nm3 |
Energy : Autothermal point |
Reducing odors with Genano RCO cased by foundry fumes
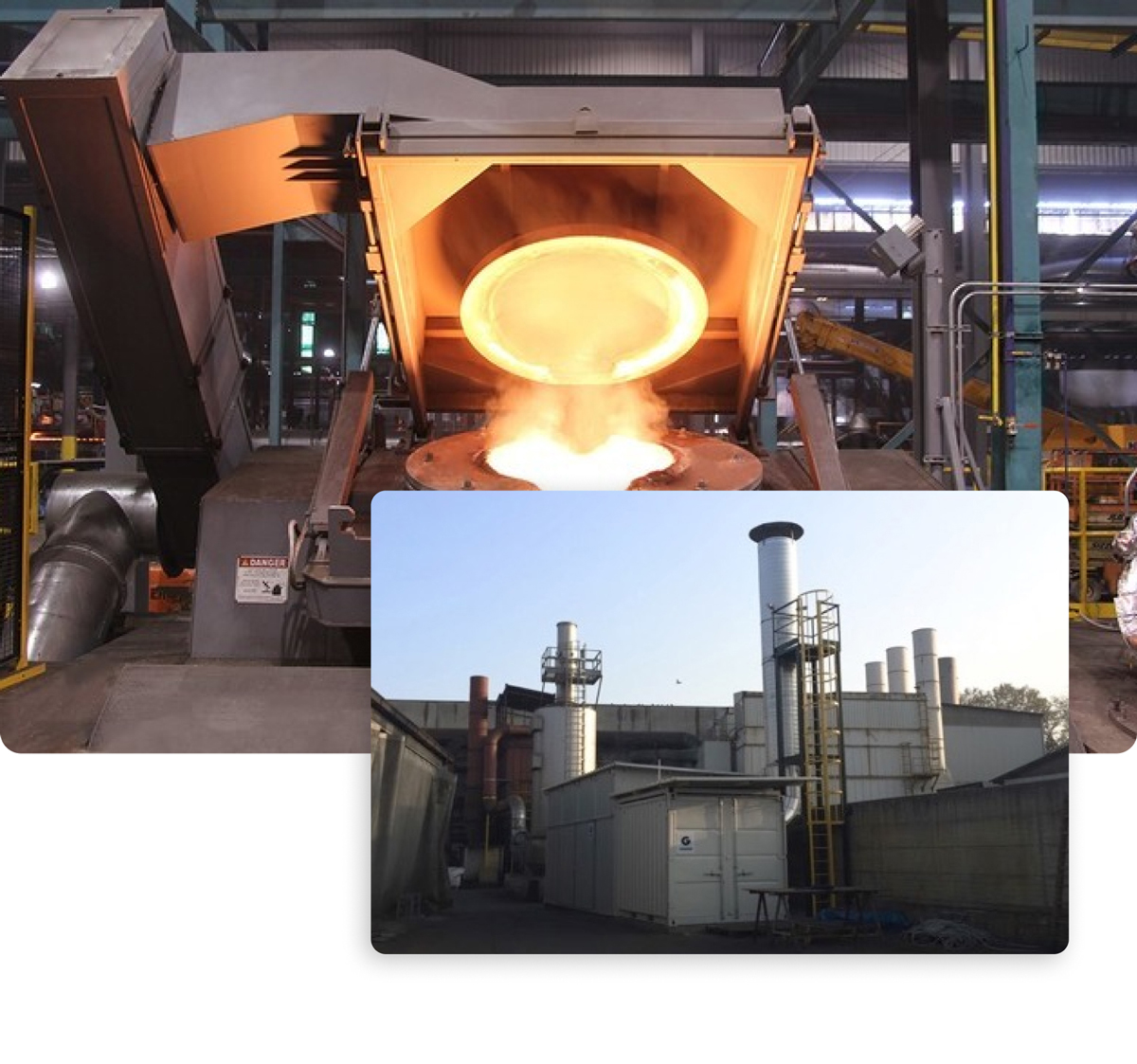
Starting point:
Advanced VOC abatement was needed for reduction of emissions and odors caused by foundry fumes.
Solution:
Installing a 3 chamber Genano regenerative catalytic oxidizer (RCO).
Result:
Emissions < 10 mgC
Process data:
Volume: 25.000 Nm3/h |
VOCs: Benzene, Toluene, Fenoli, Aldeidi, CO |
Concentration: 150-800 mg/Nm3 |
Energy: 39.730 €/year |
Sustainable choice for VOC abatement in adhesive glue production
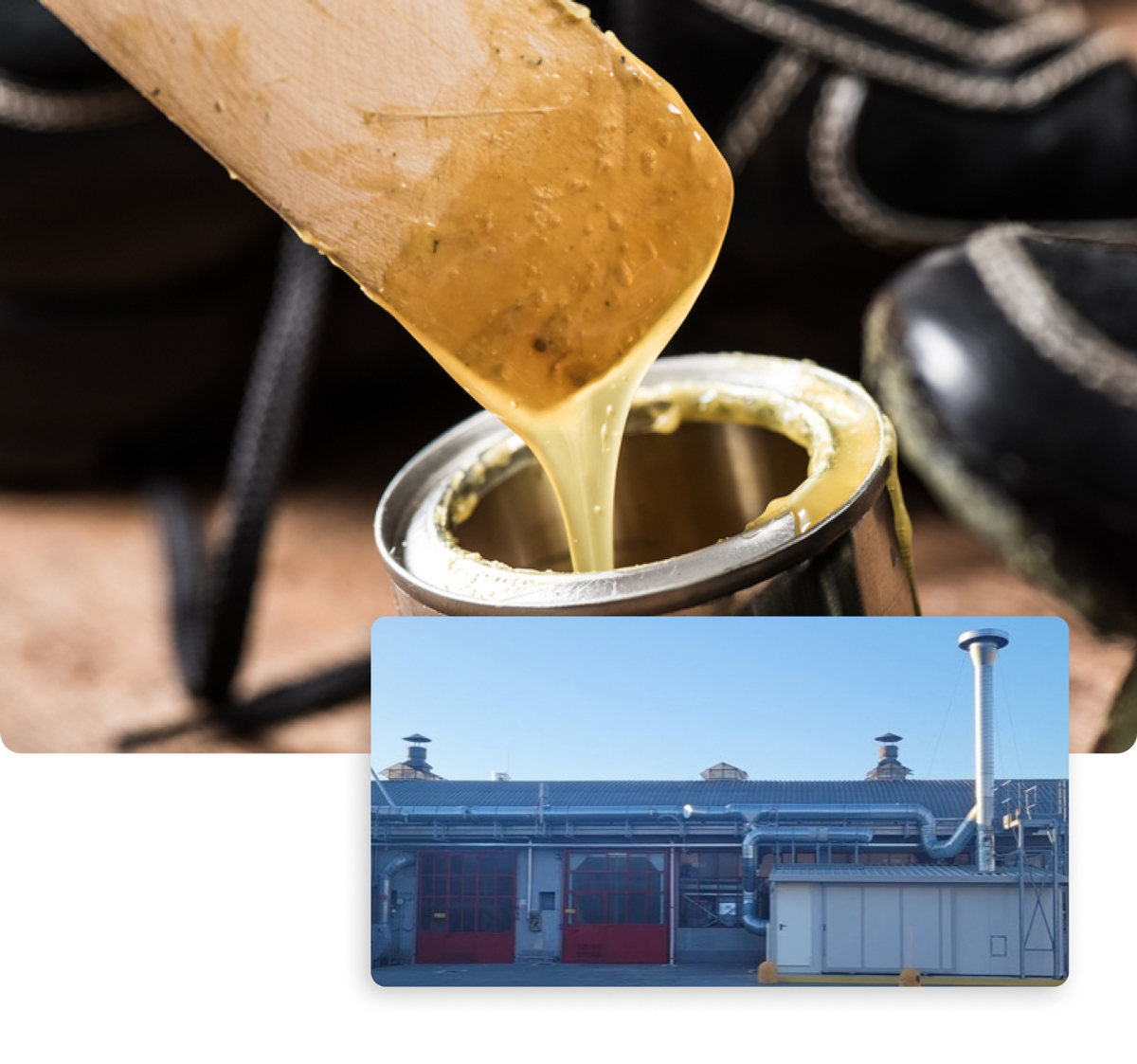
Starting point:
Increased adhesive glue production combined with stricter emission limits drove the company to search for an innovative and sustainable solution for emission abatement.
Solution:
A 3 chamber Genano regenerative catalytic oxidizer (RCO).
Result:
Emissions < 50 mgC
Process data:
Volume: 9.000 Nm3/h |
VOCs: Ciclohexane, Ethyl, Acetone |
Concentration: 1800-5000 mg/Nm3 |
Energy: Autothermal point |
Request a tailored VOC abatement and energy saving calculation or reach out for further questions: